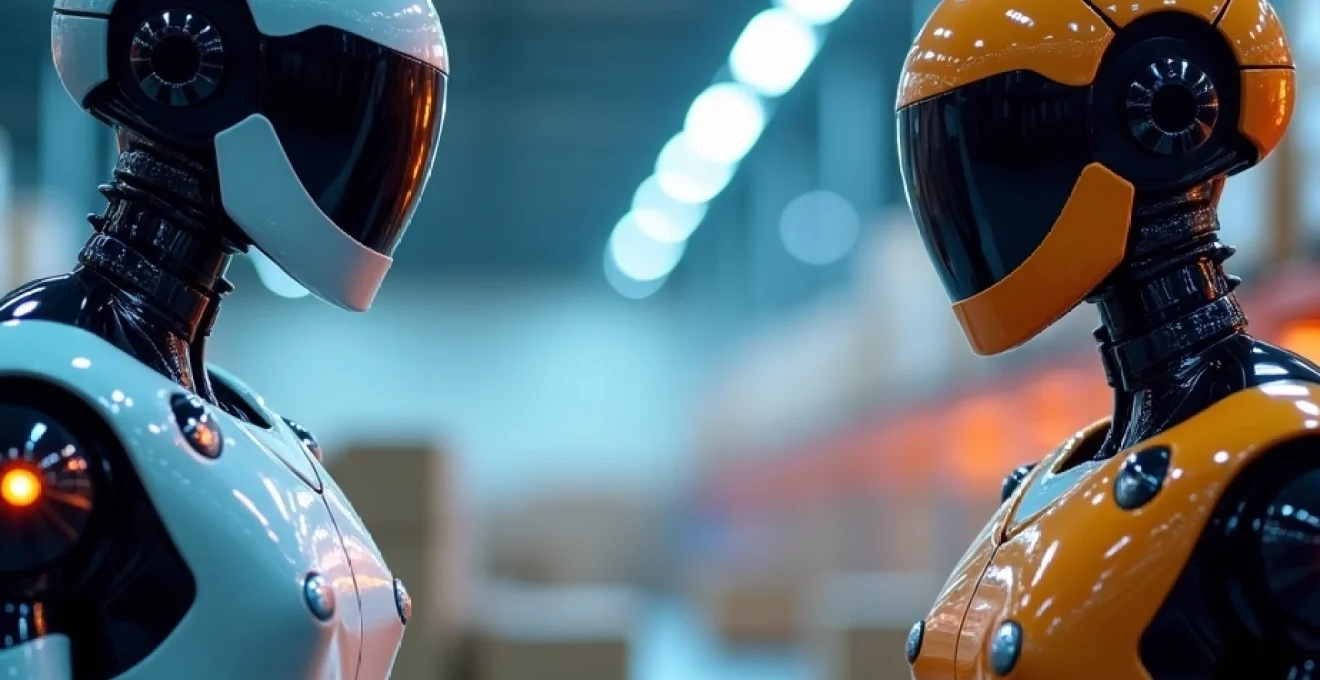
La révolution robotique est en marche dans les usines et entrepôts du monde entier. Des robots collaboratifs aux drones autonomes, en passant par l'intelligence artificielle et la modélisation 3D, les technologies de pointe transforment radicalement les processus industriels et logistiques. Cette modernisation apporte des gains considérables en termes d'efficacité, de précision et de productivité, tout en ouvrant de nouvelles perspectives pour l'avenir de l'industrie. Explorons ensemble comment ces innovations robotiques façonnent le paysage industriel et logistique d'aujourd'hui et de demain.
Robots collaboratifs optimisent les processus industriels
L'émergence des robots collaboratifs, ou cobots, marque un tournant dans l'automatisation industrielle. Contrairement aux robots traditionnels isolés dans des cages de sécurité, ces nouveaux assistants travaillent main dans la main avec les opérateurs humains. Leur conception ergonomique et leurs capteurs avancés leur permettent d'interagir en toute sécurité avec leur environnement, ouvrant la voie à une collaboration homme-machine inédite sur les chaînes de production.
Robots mobiles autonomes dans les usines
Les robots mobiles autonomes (AMR) révolutionnent la logistique interne des usines. Équipés de capteurs et de systèmes de navigation avancés, ces robots se déplacent librement dans les ateliers pour transporter matériaux et pièces. Ils optimisent les flux de production en assurant un approvisionnement continu des postes de travail, réduisant ainsi les temps d'arrêt et augmentant la productivité globale.
Ces AMR utilisent des algorithmes sophistiqués pour planifier leurs trajets et éviter les obstacles. Ils peuvent communiquer entre eux et avec les systèmes de gestion de l'usine pour coordonner leurs mouvements de manière optimale. Certains modèles sont même capables d'apprendre et d'améliorer leurs performances au fil du temps grâce à l'intelligence artificielle.
Cobots assistent les opérateurs humains
Les cobots apportent une flexibilité inégalée aux lignes de production. Faciles à programmer et à redéployer, ils s'adaptent rapidement aux changements de production. Leurs capteurs de force leur permettent de manipuler des objets fragiles avec délicatesse, tandis que leur précision constante garantit une qualité optimale.
Un exemple concret est l'utilisation de cobots pour le vissage de précision dans l'industrie électronique. Le robot assure un couple de serrage parfaitement calibré, tandis que l'opérateur supervise l'opération et gère les cas particuliers. Cette synergie homme-machine combine les atouts de chacun pour une efficacité maximale.
Bras robotisés pour tâches répétitives
Les bras robotisés industriels excellent dans l'exécution de tâches répétitives à haute cadence. Que ce soit pour le soudage, l'assemblage ou la manutention, ces robots infatigables assurent une productivité et une qualité constantes 24h/24. Leur précision micrométrique permet de réaliser des opérations complexes impossibles à la main.
Dans l'industrie automobile par exemple, des dizaines de bras robotisés travaillent de concert pour assembler un véhicule. Chaque robot exécute sa tâche spécifique avec une synchronisation parfaite, permettant de produire une voiture toutes les 60 secondes sur certaines lignes ultra-optimisées.
La productivité des cobots industriels a permis d'augmenter la productivité de 25% en moyenne, tout en améliorant les conditions de travail des opérateurs.
Automatisation robotique des entrepôts logistiques
La robotisation transforme également en profondeur le secteur de la logistique. Les entrepôts modernes font de plus en plus appel à des solutions robotisées pour optimiser leurs opérations, de la réception des marchandises à leur expédition. Cette automatisation permet de traiter des volumes croissants de commandes avec une rapidité et une précision inégalées.
Robots de prélèvement et stockage
Les robots de prélèvement et stockage, ou picking robots, révolutionnent la préparation de commandes. Équipés de systèmes de vision et de préhenseurs sophistiqués, ces robots peuvent identifier, saisir et déposer une grande variété d'articles avec dextérité. Ils naviguent de manière autonome dans les allées pour prélever les produits commandés et les placer dans les bacs ou cartons correspondants.
Ces robots utilisent l'intelligence artificielle pour optimiser leurs mouvements et s'adapter à différentes formes et tailles d'objets. Certains modèles avancés peuvent même apprendre à manipuler de nouveaux articles par simple démonstration, sans nécessiter de reprogrammation complexe.
Convoyeurs intelligents trient les colis
Les systèmes de tri automatisés basés sur des convoyeurs intelligents permettent de gérer efficacement les flux de colis dans les grands centres logistiques. Des scanners lisent les codes-barres ou étiquettes RFID des colis pour déterminer leur destination. Les convoyeurs orientent ensuite automatiquement chaque colis vers le bon quai d'expédition ou la bonne zone de stockage.
Ces systèmes peuvent trier jusqu'à 30 000 colis par heure avec un taux d'erreur inférieur à 0,1%. Ils s'adaptent en temps réel aux variations de flux grâce à des algorithmes d'optimisation sophistiqués. Certains convoyeurs intelligents intègrent même des balances pour vérifier le poids des colis et détecter d'éventuelles anomalies.
Drones inventorient les stocks rapidement
Les drones autonomes révolutionnent la gestion des stocks dans les entrepôts de grande taille. Équipés de caméras haute résolution et de lecteurs RFID, ces drones peuvent survoler les rayonnages pour réaliser un inventaire complet en quelques heures, là où il faudrait plusieurs jours à une équipe humaine.
Les données collectées sont analysées en temps réel pour identifier les éventuelles erreurs de stock ou les produits mal placés. Cette technologie permet non seulement de gagner un temps précieux, mais aussi d'améliorer significativement la précision des inventaires, réduisant ainsi les ruptures de stock et les erreurs de préparation.
L'utilisation de drones pour l'inventaire a permis de réduire le temps d'inventaire de 90% et d'améliorer la précision des stocks de 99,9% dans certains entrepôts de grande distribution.
IA pilote les robots industriels avancés
L'intelligence artificielle (IA) joue un rôle central dans l'évolution des robots industriels. Les algorithmes d'apprentissage automatique permettent aux robots de s'adapter à leur environnement, d'optimiser leurs mouvements et même de prendre des décisions complexes de manière autonome.
Dans les usines connectées, l'IA analyse en temps réel les données issues de multiples capteurs pour orchestrer le travail des robots. Elle peut par exemple ajuster les paramètres de production en fonction de la qualité des matières premières ou répartir dynamiquement les tâches entre différents robots pour optimiser les flux.
Les capacités de vision artificielle basées sur l'IA permettent aux robots d'identifier et de manipuler des objets avec une précision accrue. Ces systèmes peuvent détecter des défauts invisibles à l'œil nu ou reconnaître des pièces complexes dans n'importe quelle orientation.
L'IA ouvre également la voie à des robots capables d'apprendre par eux-mêmes. Par exemple, un robot de soudage équipé d'algorithmes d'apprentissage par renforcement peut optimiser ses paramètres au fil des opérations pour obtenir des soudures de qualité optimale, même sur des pièces aux géométries complexes.
Modélisation 3D accélère la robotisation industrielle
La modélisation 3D et la simulation numérique jouent un rôle crucial dans l'accélération du déploiement de solutions robotisées dans l'industrie. Ces technologies permettent de concevoir, tester et optimiser les systèmes robotiques avant même leur mise en œuvre physique, réduisant ainsi considérablement les délais et les coûts de développement.
Jumeaux numériques simulent les robots
Les jumeaux numériques sont des répliques virtuelles exactes des robots et de leur environnement de travail. Ces modèles 3D dynamiques permettent de simuler avec précision le comportement des robots dans différentes conditions. Les ingénieurs peuvent ainsi tester et affiner les programmes robotiques, optimiser les trajectoires et détecter d'éventuels problèmes avant la mise en production.
Cette approche réduit considérablement les temps d'arrêt lors de l'installation de nouveaux systèmes robotiques. Elle permet également d'optimiser en continu les performances des robots existants en testant de nouvelles configurations virtuellement avant de les appliquer dans le monde réel.
Conception robotique assistée par ordinateur
Les outils de conception assistée par ordinateur (CAO) spécialisés pour la robotique facilitent grandement le travail des ingénieurs. Ces logiciels permettent de concevoir des cellules robotisées complètes, en intégrant tous les éléments : robots, outils, convoyeurs, barrières de sécurité, etc.
Les fonctionnalités avancées de ces outils incluent la simulation cinématique des mouvements robotiques, l'analyse des temps de cycle et la vérification des collisions. Certains logiciels proposent même des bibliothèques de composants robotiques prêts à l'emploi, accélérant ainsi le processus de conception.
Prototypage virtuel avant implémentation réelle
Le prototypage virtuel permet de tester et d'affiner les concepts robotiques sans avoir à construire de coûteux prototypes physiques. Les ingénieurs peuvent ainsi explorer rapidement différentes configurations et optimiser leurs designs avant de passer à la fabrication.
Cette approche est particulièrement précieuse pour les projets complexes impliquant plusieurs robots travaillant de concert. La simulation permet de valider la synchronisation des mouvements et d'optimiser les flux de production de manière globale.
Le prototypage virtuel a permis de réduire de 40% en moyenne le temps de développement et de mise en œuvre des nouvelles cellules robotisées dans l'industrie automobile.
Robots industriels connectés à l'internet des objets
L'intégration des robots industriels dans l'écosystème de l'Internet des Objets (IoT) ouvre de nouvelles perspectives pour l'optimisation des processus de production. Les robots connectés peuvent échanger des données en temps réel avec d'autres machines, systèmes de gestion et même avec les produits eux-mêmes.
Cette connectivité permet une coordination parfaite entre les différents éléments de la chaîne de production. Par exemple, un robot d'assemblage peut recevoir des informations en temps réel sur la qualité des composants qu'il manipule et ajuster ses paramètres en conséquence.
L'IoT facilite également la maintenance prédictive des robots. Des capteurs surveillent en permanence l'état des composants critiques et transmettent ces données à des systèmes d'analyse avancés. Ceux-ci peuvent prédire les pannes potentielles et planifier les interventions de maintenance au moment le plus opportun, minimisant ainsi les temps d'arrêt.
La collecte et l'analyse des données issues des robots connectés permettent d'identifier des opportunités d'optimisation à l'échelle de l'usine entière. Les gestionnaires peuvent ainsi prendre des décisions éclairées pour améliorer l'efficacité globale des opérations.
Enfin, les robots connectés à l'IoT s'intègrent parfaitement dans le concept d'usine intelligente. Ils peuvent s'adapter automatiquement aux changements de production, communiquer avec les systèmes de gestion des stocks et même interagir directement avec les commandes clients pour une personnalisation poussée des produits.
L'adoption croissante de ces technologies robotiques avancées transforme en profondeur le paysage industriel et logistique. Les gains en efficacité, flexibilité et qualité sont considérables, permettant aux entreprises de relever les défis d'un marché en constante évolution. Cependant, cette révolution soulève également des questions importantes en termes d'emploi, de formation et d'éthique. Il est crucial que l'industrie aborde ces enjeux de manière proactive pour assurer une transition harmonieuse vers l'usine du futur.