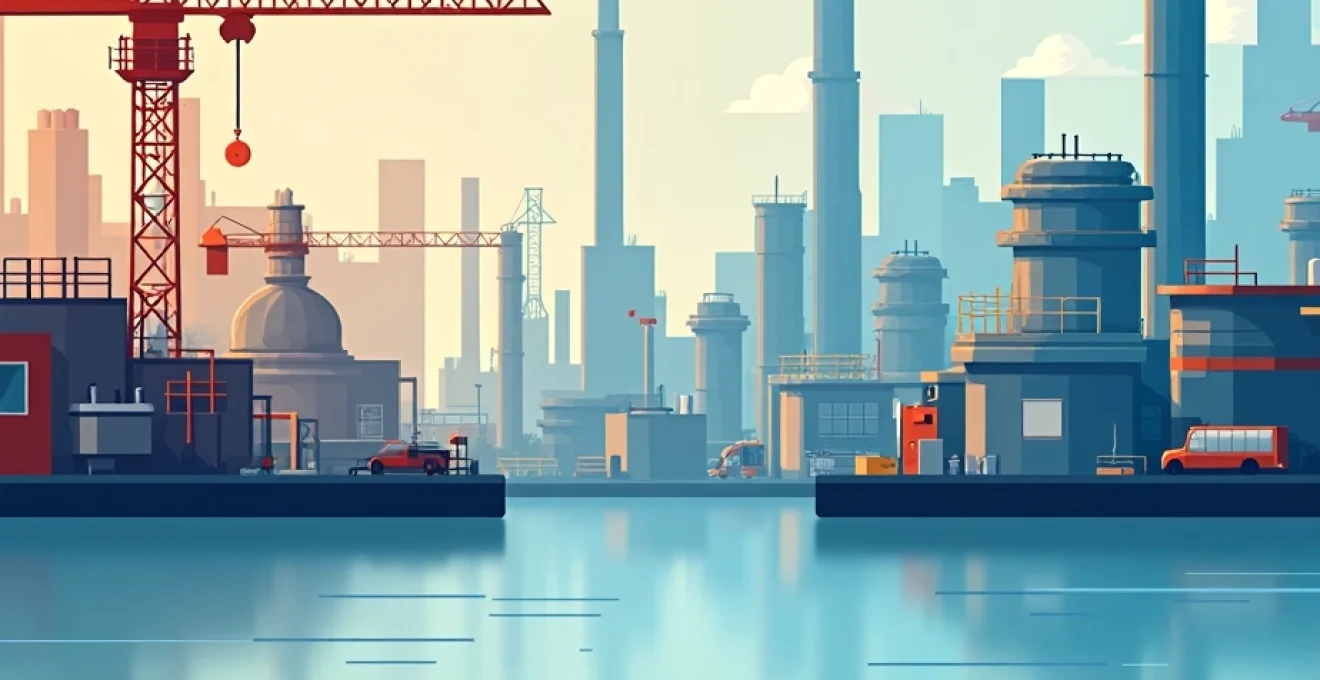
La sécurité industrielle est un pilier fondamental pour toute entreprise opérant dans le secteur manufacturier ou de production. Elle englobe un ensemble de pratiques, de procédures et de technologies visant à protéger les travailleurs, les installations et l'environnement contre les risques inhérents aux activités industrielles. Dans un monde où l'innovation technologique avance à grands pas, la mise en place d'une stratégie de sécurité robuste est plus cruciale que jamais. Elle permet non seulement de préserver la santé et le bien-être des employés, mais aussi d'optimiser les processus de production et de renforcer la réputation de l'entreprise.
Principes fondamentaux de la sécurité industrielle
La sécurité industrielle repose sur plusieurs principes clés qui guident son application au quotidien. Le premier de ces principes est la prévention. Il s'agit d'anticiper les risques potentiels avant qu'ils ne se matérialisent en accidents. Cette approche proactive implique une vigilance constante et une culture de la sécurité partagée par tous les acteurs de l'entreprise, du dirigeant à l'opérateur de ligne.
Un autre principe essentiel est celui de la hiérarchie des contrôles. Cette méthode systématique vise à éliminer ou à réduire les risques selon un ordre de priorité bien défini. Elle commence par l'élimination pure et simple du danger, suivie de la substitution par des alternatives moins dangereuses. Viennent ensuite les contrôles techniques, les contrôles administratifs et enfin, l'utilisation d'équipements de protection individuelle (EPI) comme dernière ligne de défense.
La formation continue et la sensibilisation des employés constituent également un pilier incontournable de la sécurité industrielle. Chaque travailleur doit être formé non seulement aux procédures de sécurité spécifiques à son poste, mais aussi à la reconnaissance des risques potentiels dans son environnement de travail. Cette vigilance partagée crée un filet de sécurité collectif qui renforce l'efficacité des mesures techniques mises en place.
Analyse et évaluation des risques en milieu industriel
L'analyse et l'évaluation des risques sont au cœur de toute démarche de sécurité industrielle efficace. Ces processus permettent d'identifier systématiquement les dangers présents dans l'environnement de travail, d'évaluer leur probabilité d'occurrence et leurs conséquences potentielles, et de déterminer les mesures de contrôle appropriées. Une analyse de risques bien menée est la pierre angulaire sur laquelle repose l'ensemble de la stratégie de sécurité d'une entreprise.
Méthode HAZOP pour l'identification des dangers opérationnels
La méthode HAZOP (Hazard and Operability Study) est une technique structurée d'identification des dangers et d'évaluation des risques opérationnels largement utilisée dans l'industrie. Elle consiste à examiner systématiquement chaque partie d'un processus ou d'un système pour découvrir comment des déviations par rapport aux conditions normales de fonctionnement peuvent se produire et quelles peuvent être leurs conséquences.
L'application de la méthode HAZOP implique généralement une équipe multidisciplinaire qui passe en revue les schémas de procédés et les procédures opérationnelles. Pour chaque élément du système, l'équipe applique une série de mots-guides (comme "plus de", "moins de", "pas de") à des paramètres spécifiques (pression, température, débit, etc.) pour identifier des scénarios potentiellement dangereux. Cette approche méthodique permet de mettre en lumière des risques qui pourraient passer inaperçus avec des méthodes moins structurées.
Utilisation de la matrice de criticité dans l'évaluation des risques
La matrice de criticité est un outil visuel puissant pour évaluer et hiérarchiser les risques identifiés. Elle combine la probabilité d'occurrence d'un événement dangereux avec la gravité de ses conséquences potentielles pour donner une estimation globale du niveau de risque. Cette représentation sous forme de tableau permet de classer les risques de manière intuitive et de prioriser les actions de prévention ou de mitigation.
Typiquement, une matrice de criticité se présente sous la forme d'un tableau à double entrée, avec la probabilité sur un axe et la gravité sur l'autre. Chaque cellule de la matrice correspond à un niveau de risque, généralement codé par couleur (vert pour faible, jaune pour moyen, rouge pour élevé). Cette visualisation facilite la communication des résultats de l'évaluation des risques à toutes les parties prenantes, y compris la direction et les opérateurs.
Mise en œuvre de l'analyse des modes de défaillance (AMDEC)
L'Analyse des Modes de Défaillance, de leurs Effets et de leur Criticité (AMDEC) est une méthode analytique utilisée pour identifier et évaluer les défaillances potentielles d'un système, d'un processus ou d'un produit. Dans le contexte de la sécurité industrielle, l'AMDEC est particulièrement utile pour anticiper les points faibles d'un équipement ou d'une procédure qui pourraient conduire à des situations dangereuses.
La mise en œuvre de l'AMDEC suit généralement les étapes suivantes :
- Identification des fonctions du système et de ses composants
- Détermination des modes de défaillance potentiels pour chaque composant
- Analyse des effets de chaque mode de défaillance
- Évaluation de la criticité de chaque défaillance
- Proposition d'actions correctives ou préventives
L'AMDEC permet non seulement d'identifier les risques, mais aussi de les quantifier et de les prioriser, ce qui en fait un outil précieux pour l'allocation des ressources de sécurité.
Intégration du facteur humain dans l'analyse des risques industriels
L'intégration du facteur humain dans l'analyse des risques est cruciale pour une compréhension complète de la sécurité industrielle. Les erreurs humaines, qu'elles soient dues à la fatigue, au stress, à un manque de formation ou à une mauvaise conception ergonomique, peuvent être à l'origine d'accidents graves. Une analyse des risques qui ne prendrait pas en compte ces aspects serait incomplète et potentiellement trompeuse.
Pour intégrer efficacement le facteur humain, il est nécessaire d'adopter une approche holistique qui considère non seulement les compétences et les comportements individuels, mais aussi l'environnement de travail, l'organisation des tâches et la culture de sécurité de l'entreprise. Des techniques comme l'analyse des tâches cognitives ou l'évaluation de la charge de travail peuvent fournir des insights précieux sur les risques liés aux interactions homme-machine.
L'analyse des risques industriels sans prise en compte du facteur humain est comme naviguer avec une carte incomplète : vous pouvez éviter certains écueils, mais vous risquez toujours de vous échouer sur des dangers invisibles.
Systèmes de gestion de la sécurité industrielle
Les systèmes de gestion de la sécurité industrielle (SGSI) sont des cadres structurés qui permettent aux organisations de gérer systématiquement leurs risques en matière de santé et de sécurité au travail. Ces systèmes intègrent politiques, procédures et pratiques pour créer un environnement de travail sûr et promouvoir une culture de la sécurité. Un SGSI efficace est essentiel pour maintenir et améliorer continuellement les performances en matière de sécurité.
Norme ISO 45001 pour le management de la santé et sécurité au travail
La norme ISO 45001 est la référence internationale pour les systèmes de management de la santé et de la sécurité au travail. Elle fournit un cadre pour l'amélioration continue de la sécurité, la réduction des risques sur le lieu de travail et la création de meilleures conditions de travail, plus sûres et plus saines. L'adoption de cette norme démontre l'engagement d'une organisation envers la sécurité de ses employés et peut améliorer sa réputation auprès des parties prenantes.
Implémentation du système LOTO (lock Out/Tag out) pour la maîtrise des énergies
Le système LOTO (Lock Out/Tag Out) est une procédure de sécurité critique utilisée pour s'assurer que les machines et équipements dangereux sont correctement arrêtés et isolés de leurs sources d'énergie avant que des travaux de maintenance ou d'entretien ne soient effectués. Cette procédure est essentielle pour prévenir les accidents liés à des démarrages inattendus ou à des libérations d'énergie stockée.
L'implémentation d'un système LOTO efficace implique plusieurs étapes :
- Identification de toutes les sources d'énergie pour chaque équipement
- Développement de procédures de consignation spécifiques
- Formation des employés aux procédures LOTO
- Fourniture d'équipements de verrouillage et d'étiquetage appropriés
- Mise en place d'un système de suivi et d'audit des procédures LOTO
Un système LOTO bien implémenté est un exemple concret de la façon dont des procédures systématiques peuvent significativement réduire les risques d'accidents graves dans l'industrie.
Digitalisation de la gestion de la sécurité avec les logiciels EHS
La digitalisation de la gestion de la sécurité à travers l'utilisation de logiciels EHS (Environnement, Hygiène et Sécurité) représente une avancée majeure dans le domaine de la sécurité industrielle. Ces outils permettent une gestion plus efficace et en temps réel des données liées à la sécurité, facilitant ainsi la prise de décision et l'amélioration continue des processus de sécurité.
Les logiciels EHS offrent généralement des fonctionnalités telles que :
- La gestion des incidents et des accidents
- Le suivi des actions correctives et préventives
- La gestion des audits et des inspections de sécurité
- Le suivi de la formation et des compétences en matière de sécurité
- La génération de rapports et d'analyses de tendances
L'adoption de ces outils numériques peut considérablement améliorer la visibilité sur les performances de sécurité et faciliter la conformité réglementaire. Cependant, il est important de noter que la technologie ne remplace pas une culture de sécurité solide ; elle doit être vue comme un facilitateur plutôt qu'une solution miracle.
Équipements de protection individuelle et collective
Les équipements de protection individuelle (EPI) et collective constituent la dernière ligne de défense contre les risques résiduels qui n'ont pas pu être éliminés ou suffisamment réduits par d'autres moyens. Bien que leur utilisation soit souvent perçue comme une contrainte, ces équipements sont essentiels pour protéger la santé et la sécurité des travailleurs dans de nombreuses situations industrielles.
Les EPI comprennent une large gamme d'équipements tels que les casques, les lunettes de sécurité, les gants, les chaussures de sécurité, les protections auditives et les équipements de protection respiratoire. Le choix des EPI appropriés doit être basé sur une évaluation approfondie des risques spécifiques à chaque tâche et environnement de travail. Il est crucial de s'assurer non seulement que les EPI sont adaptés aux risques, mais aussi qu'ils sont confortables et correctement ajustés pour encourager leur utilisation systématique par les employés.
Les équipements de protection collective, quant à eux, visent à protéger l'ensemble des travailleurs dans une zone donnée. Ils incluent des dispositifs tels que les systèmes de ventilation, les barrières de sécurité, les dispositifs anti-chute collectifs et les systèmes d'extinction d'incendie automatiques. Ces mesures sont généralement préférables aux EPI car elles offrent une protection plus large et ne dépendent pas de l'action individuelle des travailleurs pour être efficaces.
La meilleure protection est celle qui ne repose pas uniquement sur le comportement individuel. Les équipements de protection collective doivent toujours être privilégiés lorsque cela est possible.
Il est important de noter que l'utilisation d'EPI ne doit pas être considérée comme une alternative à la mise en place de mesures de contrôle plus fondamentales. Elle doit s'inscrire dans une stratégie globale de gestion des risques, en complément d'autres mesures telles que l'élimination des dangers à la source, la mise en place de barrières techniques et l'amélioration des procédures de travail.
Formation et sensibilisation à la sécurité industrielle
La formation et la sensibilisation sont des composantes essentielles de tout programme de sécurité industrielle efficace. Elles visent à doter les employés des connaissances, des compétences et des attitudes nécessaires pour travailler en toute sécurité et pour reconnaître et réagir aux dangers potentiels. Une formation adéquate peut significativement réduire le nombre d'accidents et améliorer la culture générale de sécurité au sein de l'organisation.
Programmes de formation CACES pour la conduite d'engins
Les Certificats d'Aptitude à la Conduite En Sécurité (CACES) sont des formations essentielles pour les opérateurs d'engins dans l'industrie. Ces programmes visent à assurer que les conducteurs d'engins possèdent les connaissances et les compétences nécessaires pour opérer en toute sécurité. La formation CACES couvre une variété d'engins, des chariots élévateurs aux grues en passant par les plateformes élévatrices.
Les programmes CACES comprennent généralement :
- Une formation théorique sur la réglementation et les principes de sécurité
- Une formation pratique sur l'utilisation spécifique de l'engin
- Une évaluation des connaissances et des compétences
- Un test pratique en conditions réelles
L'obtention du CACES n'est pas seulement une obligation légale pour de nombreux postes, c'est aussi un gage de professionnalisme et de sécurité accrue sur les chantiers et dans les entrepôts. Les employeurs qui investissent dans ces formations démontrent leur engagement envers la sécurité de leurs employés et la prévention des accidents liés à l'utilisation d'engins.
Simulations et exercices pratiques pour la gestion des situations d'urgence
Les simulations et exercices pratiques jouent un rôle crucial dans la préparation des employés à faire face aux situations d'urgence en milieu industriel. Ces exercices permettent de tester les procédures d'urgence, d'identifier les faiblesses potentielles et d'améliorer la réactivité du personnel en cas de crise réelle.
Parmi les scénarios couramment simulés, on trouve :
- Les incendies et évacuations
- Les déversements de produits chimiques
- Les accidents de personnes
- Les pannes d'équipements critiques
Ces exercices ne se limitent pas à la simple exécution de procédures. Ils visent également à développer les compétences de prise de décision sous pression et de communication en situation de stress. L'analyse post-exercice est tout aussi importante que l'exercice lui-même, permettant d'identifier les points d'amélioration et d'ajuster les plans d'urgence en conséquence.
Utilisation de la réalité virtuelle dans la formation à la sécurité
La réalité virtuelle (RV) émerge comme un outil puissant pour la formation à la sécurité industrielle. Cette technologie offre la possibilité de créer des environnements de formation immersifs où les employés peuvent expérimenter des situations dangereuses sans risque réel. L'utilisation de la RV dans la formation à la sécurité présente plusieurs avantages :
- Simulation réaliste de scénarios dangereux
- Répétition illimitée des exercices sans coût supplémentaire
- Personnalisation des scénarios selon les besoins spécifiques de l'entreprise
- Engagement accru des apprenants grâce à l'aspect interactif
Par exemple, un opérateur peut s'entraîner à réagir à une fuite de gaz toxique ou à un incendie dans un environnement virtuel, développant ainsi ses réflexes et sa confiance avant d'être confronté à une situation réelle. Cette approche améliore non seulement la rétention des connaissances mais permet aussi de réduire le temps et les coûts associés aux formations traditionnelles.
Réglementation et normes de sécurité industrielle
La réglementation et les normes de sécurité industrielle forment le cadre légal et technique dans lequel les entreprises doivent opérer pour assurer la sécurité de leurs employés et de leur environnement. Ces règles, souvent issues de leçons apprises à la suite d'accidents industriels majeurs, évoluent constamment pour s'adapter aux nouveaux risques et technologies.
Directive seveso III et prévention des accidents majeurs
La directive Seveso III est un pilier de la réglementation européenne en matière de prévention des accidents industriels majeurs. Nommée d'après la catastrophe de Seveso en Italie en 1976, cette directive vise à prévenir les accidents impliquant des substances dangereuses et à limiter leurs conséquences pour la santé humaine et l'environnement.
Les principales exigences de la directive Seveso III incluent :
- L'identification et le classement des établissements à risques
- La mise en place de systèmes de gestion de la sécurité
- L'élaboration de plans d'urgence internes et externes
- L'information du public sur les risques et les mesures de sécurité
Les entreprises soumises à cette directive doivent démontrer qu'elles ont pris toutes les mesures nécessaires pour prévenir les accidents majeurs et limiter leurs conséquences. Cela implique une évaluation rigoureuse des risques, la mise en place de barrières de sécurité multiples et une communication transparente avec les autorités et le public.
Application des normes ATEX en zones à risque d'explosion
Les normes ATEX (ATmosphères EXplosives) régissent la protection des travailleurs contre les risques d'explosion dans les environnements industriels. Ces normes s'appliquent aux équipements et systèmes de protection destinés à être utilisés en atmosphères explosibles, qu'il s'agisse de gaz, de vapeurs ou de poussières combustibles.
L'application des normes ATEX implique :
- Le zonage des aires à risque d'explosion
- La sélection d'équipements certifiés ATEX adaptés à chaque zone
- La formation du personnel aux risques spécifiques
- La mise en place de procédures de travail sécurisées
Le respect des normes ATEX est crucial dans de nombreux secteurs industriels, notamment la pétrochimie, l'agroalimentaire et la métallurgie. Il exige une vigilance constante et une mise à jour régulière des évaluations de risques et des équipements utilisés.
Conformité aux exigences de la directive machines 2006/42/CE
La directive machines 2006/42/CE établit les exigences essentielles de santé et de sécurité relatives à la conception et à la construction des machines dans l'Union européenne. Son objectif est de garantir un niveau élevé de protection pour les utilisateurs de machines tout en assurant la libre circulation des équipements au sein du marché unique européen.
Les principaux aspects de la conformité à la directive machines incluent :
- L'évaluation des risques dès la conception de la machine
- L'intégration de la sécurité dans la conception (sécurité intrinsèque)
- La fourniture d'informations sur les risques résiduels
- L'élaboration d'une documentation technique complète
- L'apposition du marquage CE sur les machines conformes
Pour les fabricants et les utilisateurs de machines industrielles, la conformité à cette directive est non seulement une obligation légale mais aussi un gage de qualité et de sécurité. Elle encourage l'innovation dans la conception de machines plus sûres et plus efficaces, contribuant ainsi à réduire les accidents du travail liés à l'utilisation de machines. La conformité réglementaire n'est pas une fin en soi, mais le point de départ d'une démarche d'amélioration continue de la sécurité industrielle. Elle fournit un cadre solide sur lequel bâtir une culture de sécurité robuste et proactive.